Test and Tag
Test and Tag Process: Ensuring Electrical Safety in the Workplace
Test and Tag is a critical safety procedure designed to ensure the safe operation of electrical equipment in workplaces.
This process involves the inspection, testing, and labeling of electrical appliances to verify compliance with relevant safety standards.
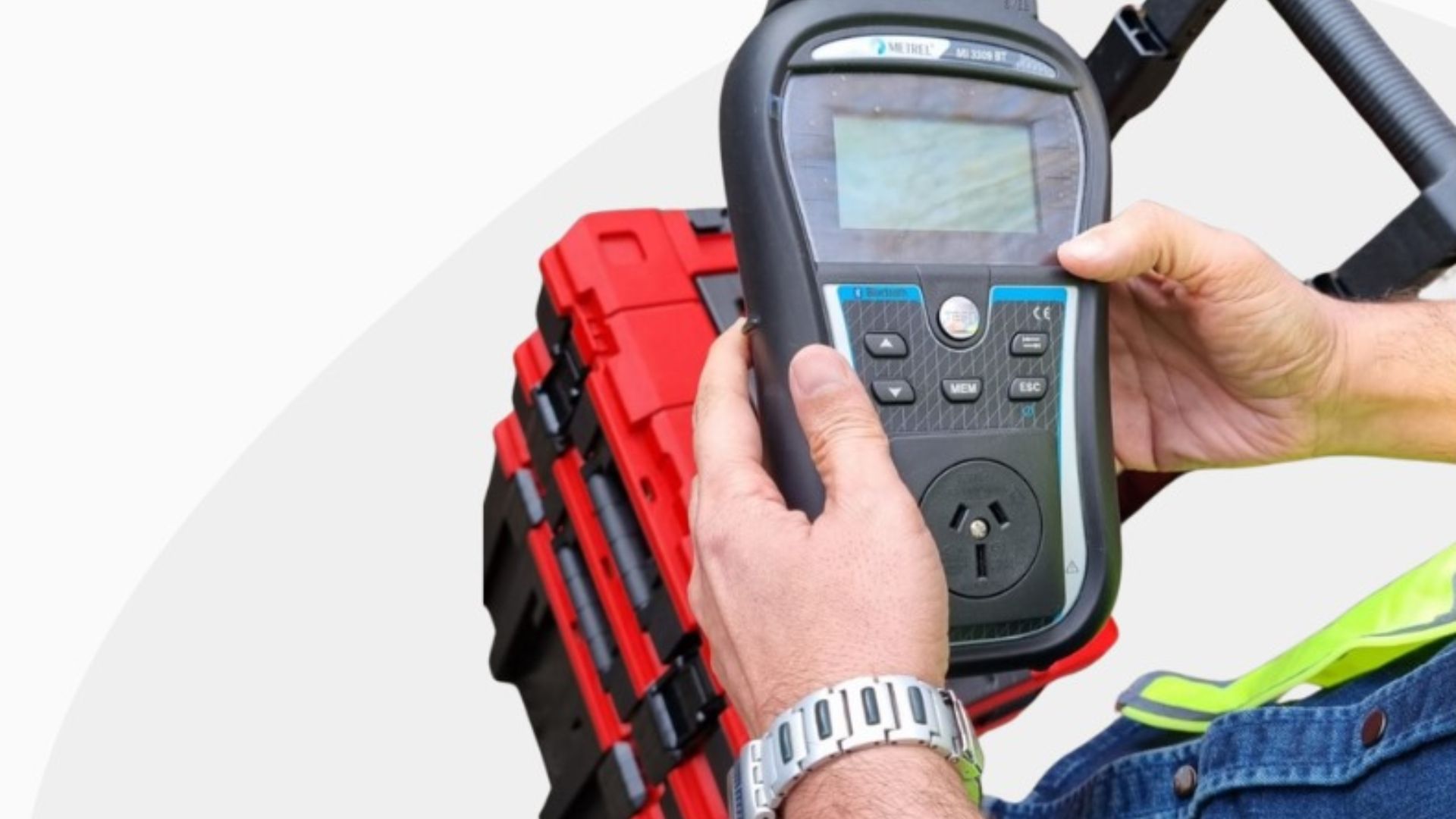
We adhere to two key standards:
- AS/NZS 3760:2022: This standard governs in-service safety inspection and testing of electrical equipment. It covers general workplaces and ensures that electrical appliances are safe for ongoing use.
- AS/NZS 3012:2019: This standard is specifically aimed at construction and demolition sites. It sets out the requirements for testing and tagging of electrical equipment in high-risk environments, ensuring enhanced safety measures where the risk of electrical hazards is greater.
Here’s a detailed breakdown of the Test and Tag process according to the AS/NZS 3760 standard:
1. Visual Inspection
We begin with a thorough visual inspection of the equipment to identify any visible damage, defects, or signs of wear that could compromise its safety.
This includes checking for issues such as damaged cords, loose connections, exposed wires, or cracked casings. Visual inspection is crucial as it helps identify potential hazards that might not be detected during electrical testing.
2. Electrical Testing
Following the visual check, we perform a series of electrical tests using calibrated testing instruments. These tests include:
- Insulation resistance testing: Verifying that the equipment’s insulation is intact and sufficient to prevent electrical leakage.
- Earth continuity testing: Ensuring the integrity of the equipment’s earthing system, which is critical for user protection in case of a fault.
- Polarity testing: Confirming that wiring in the device is correctly connected and aligned with the standard configuration, which helps prevent short circuits or electrical hazards.
3. Tagging and Labeling
After successfully passing both visual and electrical tests, we apply a durable, tamper-resistant label (or tag) to the equipment. This label provides essential information including:
• Test date
• Next scheduled test date
• Tester’s identification This tagging system ensures easy traceability and helps businesses stay compliant with safety regulations by indicating when the next test is due.
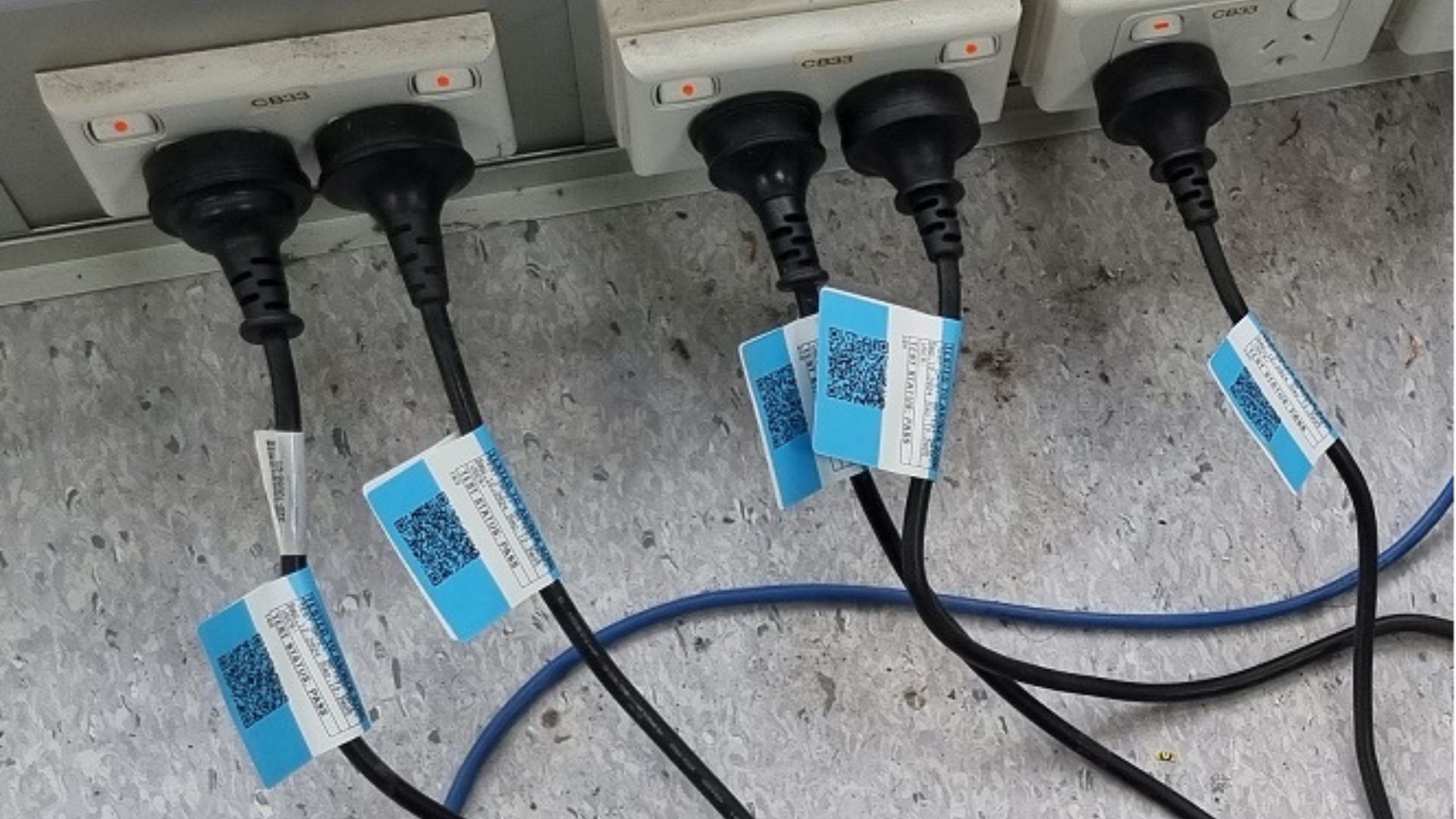
4. Record Keeping
For compliance and audit purposes, we maintain accurate and confidential records of all tests conducted. These records include:
• Device identification (serial numbers, asset codes, etc.)
• Test results for each piece of equipment
• Actions taken, such as repairs or replacements Our systematic record-keeping ensures that customers can easily retrieve historical data for regulatory reviews or internal safety audits.
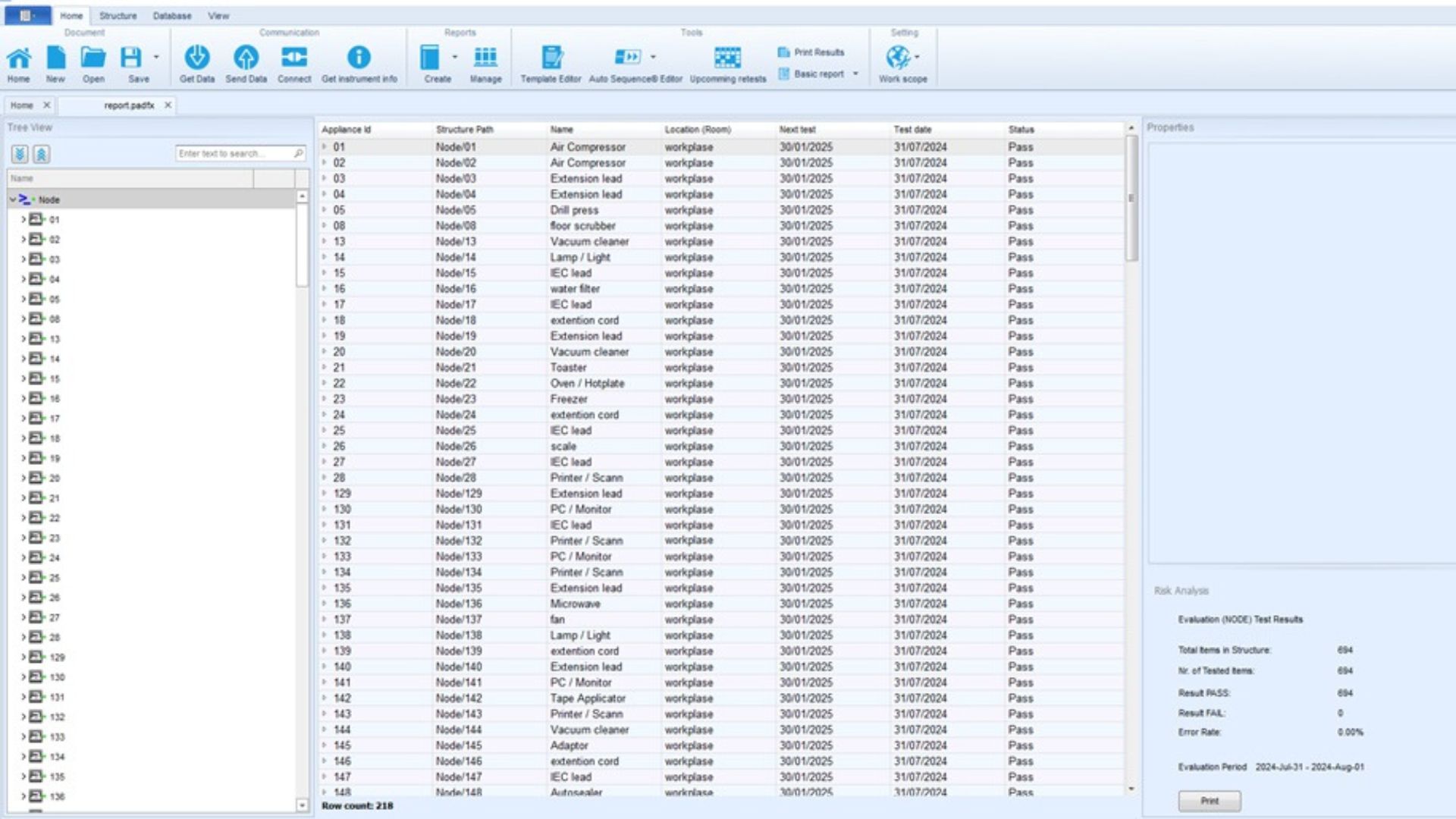
5. Retesting Schedules
Retesting is not a one-time process. We establish retesting schedules based on the type of equipment and its operating environment. High-risk environments, such as construction sites, may require more frequent testing, while equipment in office settings might have a longer retesting interval.
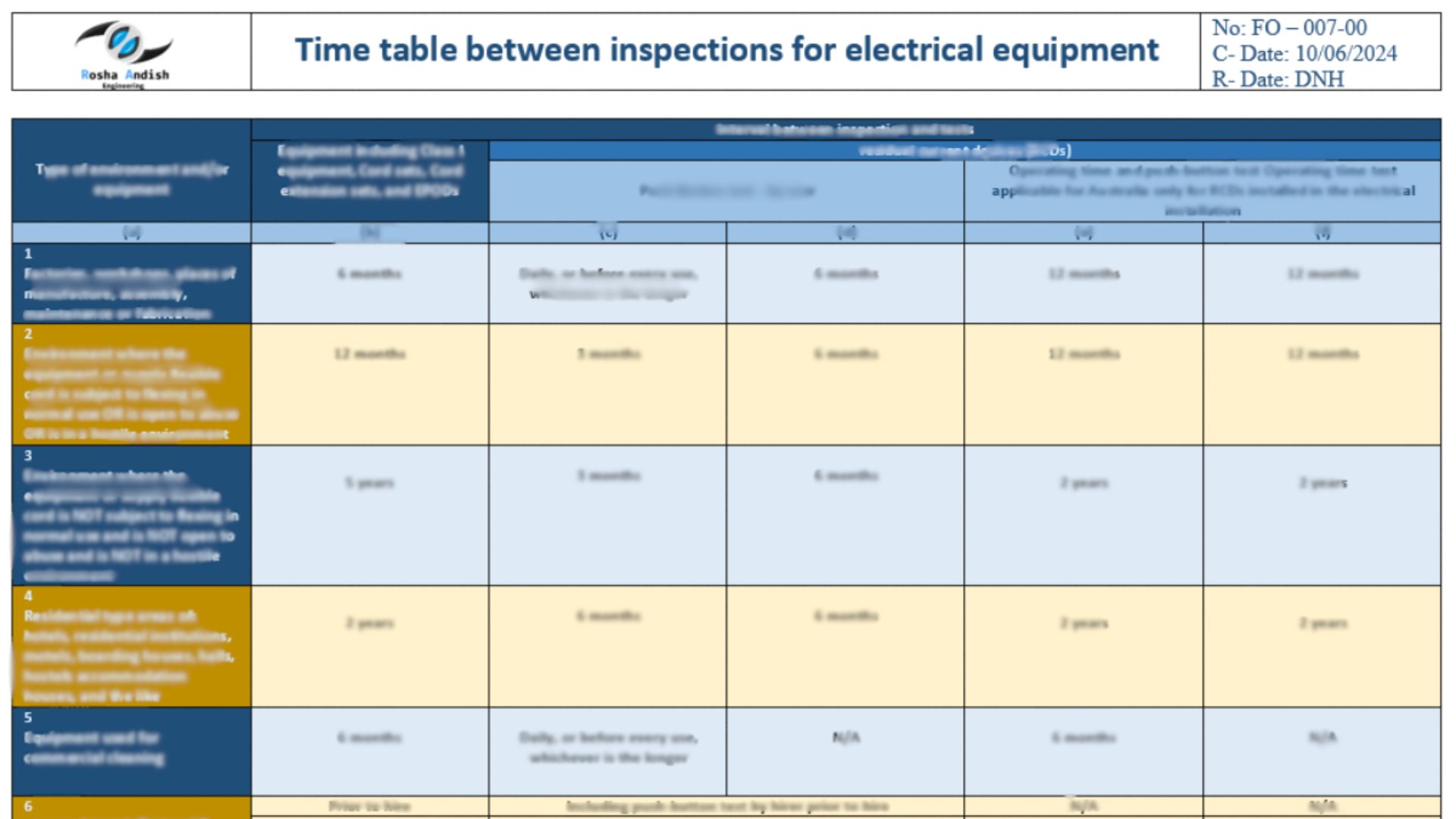
6. Detailed Documentation
After testing, we provide customers with a comprehensive test report. This report outlines the findings, including any recommendations for maintenance, repairs, or equipment replacement to keep their workplace safe and compliant with safety standards. The inspection reports are generated using the latest version of the industry-leading software, ensuring accuracy, clarity, and compliance with the most up-to-date reporting formats available in the market.
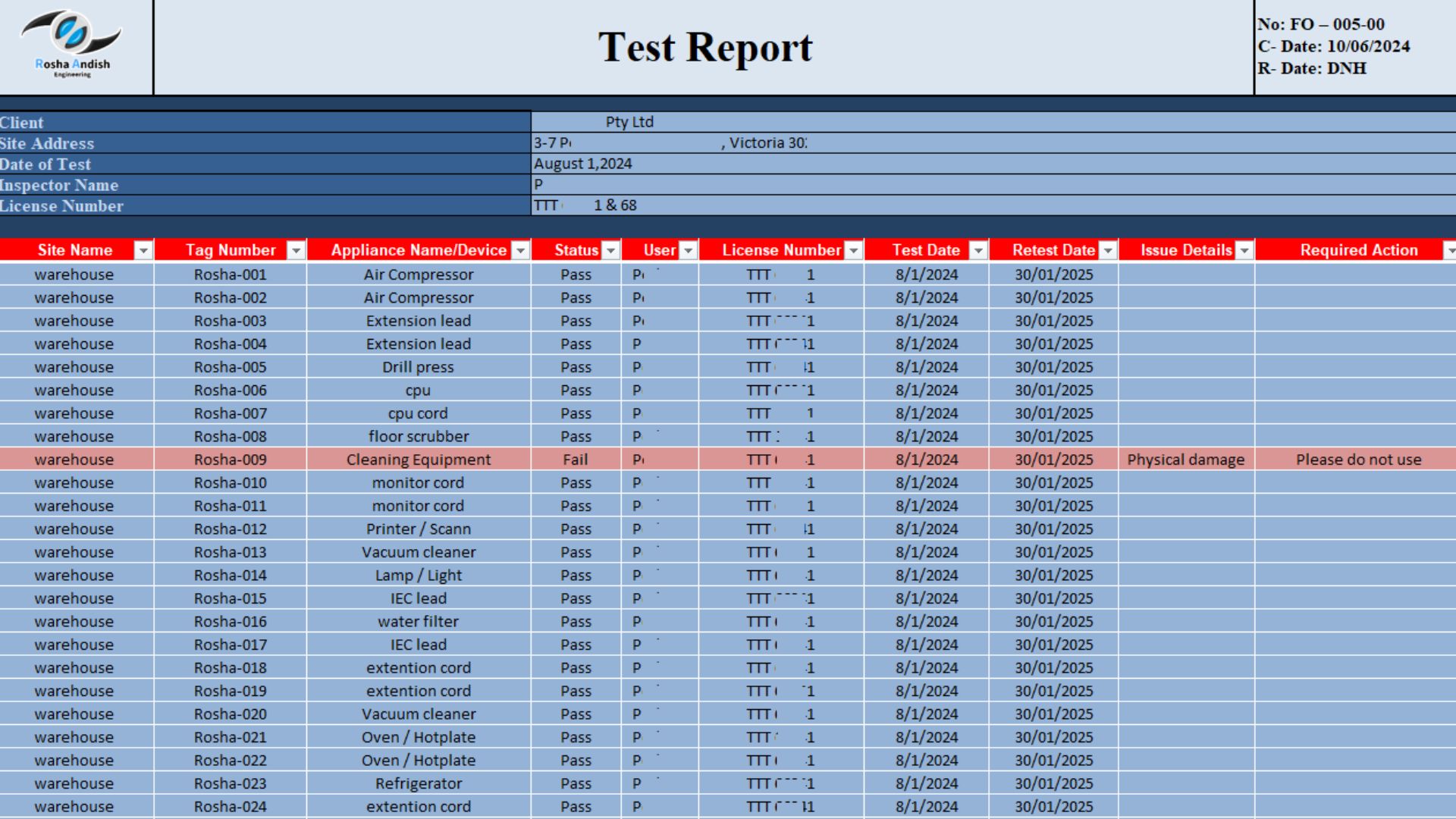
Standards Compliance
All our Test and Tag activities are performed under the stringent guidelines of the ISO 9001:2015 Quality Management Standard and the ISO/IEC 17020:2012 standard for inspection bodies. This ensures that our testing procedures are consistent, reliable, and meet international benchmarks for quality and safety.
By adhering to these rigorous processes, we help businesses maintain the highest level of electrical safety, reduce the risk of electrical accidents, and remain compliant with occupational health and safety regulations.